Interview with Blandine Laborie (EMBA 2017), Quality Assurance Director of Research & Innovation at L'Oréal
After nearly six years spent as Quality Assurance Director for cosmetic brands owned by LVMH, Blandine Laborie (Executive MBA 2017) was offered the chance to take up a newly created position in September 2024 with similar responsibilities in research and innovation (R&I) at L’Oréal. Here she tells us about her daily life in a fascinating but little known profession, where science and risk management come together in a context of constant collaboration between departments facing distinct challenges on a competitive market in the race for innovation.
How would you summarise your current position and responsibilities?
My work is highly cross-departmental. Quality assurance in R&I plays a support role in the design of products with a view to their industrialization and ultimately their release on the market. We make sure we bring consumers innovative products in compliance with applicable safety regulations and which fulfil a marketing promise made upstream. Our work includes putting in place processes as well as project and risk management. The EMBA offered at EDHEC has given me a business-oriented vision to complement my initial education in engineering – which is the type of profile I mostly supervise today. I report to the Director of Operational Excellence, indicative of just how important quality assurance is at L’Oréal.
What is so specific about R&I at L’Oréal?
L’Oréal runs research operations involving more than 4000 people across 7 innovation hubs (US, Brazil, China, India, Japan, South Africa and France). What makes it so specific is that it involves advanced research with 700 international researchers, experts in skin and hair who publish papers in prestigious scientific journals and collaborate with major universities. They work closely with our suppliers of raw materials to develop new assets to be used in the design of innovative products. As product development advances, we increasingly interact with the marketing and operational staff teams. The quality assurance department ensures the reliability and robustness of the design process while maintaining creativity, the central element of our work. It provides a structured framework with processes and methods so that we can navigate risks together. Far from being limited to drafting procedures and conducting checks, quality assurance aims to protect the reputation of L'Oréal, stimulate innovation and optimise time to market in an increasingly competitive environment.
So marketing is really the point of departure …
The point of departure is listening to the needs and aspirations of consumers and the specificities of their skin type, hair and beauty rituals. The activities of the quality assurance department are not driven by marketing. In our support role, we intervene downstream to ensure the compliance of finished products before they are made available to operational staff (industrialization) and, finally, to consumers. The cosmetics market is subject to strict regulations specific to each country, particularly in China, Europe and the US. These impose the most rigorous structure on our activities. Many independent brands innovate very quickly and are very agile because often they don't adhere to the same standards as us. As a leading firm in its industry, L'Oréal must be competitive, offering unique innovations with strong performance while at the same time respecting its own very high demands in terms of quality and safety. In a climate where consumers are constantly looking for more natural ingredients, transparency and traceability, and where influencers are testing our products, quality assurance plays a fundamental role: we help structure, simplify and facilitate collaboration between staff teams so we can step up and meet the demands of this complex and highly dynamic sector.
What do you need to constantly focus on in quality assurance?
In R&I, risk management is of the utmost importance because innovation intrinsically means risk-taking. The design quality team provide methods to assess risks associated with a new formula as soon as the initial product development phases begin. My role is to bring together the various experts, including from marketing, and stakeholders to evaluate these risks and guarantee an industrialization process without any hiccups. The aim is to anticipate problems by identifying a series of specific decision-making milestones.
You were responsible for crisis management for 7 years at Danone …
My experience at Danone allowed me to develop expertise in handling exceptional situations, skills that are now invaluable to me at L'Oréal. Anticipation and preparation are key: we rely on rigorous processes and best practises to understand the facts, bring together the right people, guarantee an effective response for the products in question, and protect the reputation of L'Oréal, even when faced with rare events. Communication, often cited in crisis management, is only the tip of the iceberg within the different logistical phases. In short, it requires anticipation and responsiveness to ensure L'Oréal’s resilience to cope with exceptional situations. We are prepared for such situations even though, thankfully, they only arise very rarely!
How is data linked to quality assurance?
Quality assurance is a true partner of digitalization, acting on two levels: ensuring the quality of data and facilitating the creation of relevant processes. Given L'Oréal’s vast wealth of data and historic know-how when it comes to research, quality assurance helps maintain the scientific rigour essential if you wish to obtain reliable data. For example, the precise calibration of equipment is essential to ensuring the usability of data generated during lab trials and the design process alongside our suppliers of raw materials. The quality assurance department also oversees the harmonisation of the protocols followed by staff teams, which also contributes to high-quality data. The digitalization processes and formats must be clearly identified and understood before any digitalization takes place. This also enables us to determine performance indicators such as the transformation rates from ideas into formulas (as well as the time it takes for a new molecule to move from advanced research to development), manage time to market, identify areas of improvement and optimise the use of resources, thus freeing up creativity.
Does quality assurance bring together principles shared by all businesses?
The overarching principles of quality assurance are indeed shared across all industries. However, the areas of expertise we rely on vary depending on the sector and specific regulations. Quality assurance is still often seen as a question of monitoring and procedures, but checks and audits, although essential, often take place too late in the value chain. It's all very well to produce documents to maintain a written record of a certain know-how, but quality assurance is above all a mindset. The main challenge I face is not to put in place tools but to instil a veritable quality assurance culture among research staff, by demonstrating that it is intrinsically linked to their mission.
Is it only possible to innovate once you have adopted these “principles”?
I believe so, especially in the current market context. Quality assurance offers a structural framework. It is an essential lever if you wish to lubricate business processes and speed up innovation. It is also a way to capitalise on feedback to avoid repeating past errors in future designs, reduce redundancies and properly allocate resources. My primary motivation is to share and promote this vision of quality in design, a key objective for L'Oréal. Quality assurance is a partner, and offers true value added to move the company forward.
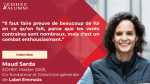
Commentaires0
Veuillez vous connecter pour lire ou ajouter un commentaire
Articles suggérés